
Dear colleagues,
Enjoy reading the SARIA Global Newsletter 4/2023.
This newsletter contains information on Group-wide news to keep you up to date and to provide specific insights and background on processes and developments.
The aim is simple: share information + get in touch = move forward together!
Your SARIA Group Communications
Looking for a translation? Behind the red buttons are websites with automated translations.
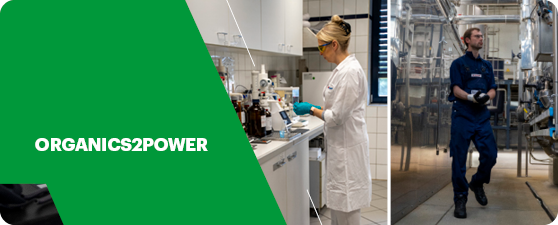
Organics2Power combines the Group-wide activities of SecAnim, ReFood and ecoMotion in the field of sustainable energy sources based on organic raw materials. Check out the latest trending topics by clicking on the red button below.
The topics are: O2Ps Zero Net CO2 fertilizer is certified // Daka at the Open Agricultural Day // ReFood Germany prepares for legislative change // ReFood Poland & ALDI . . .
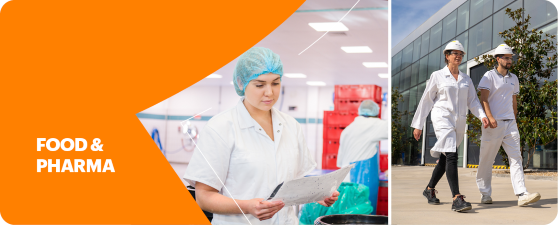
Food & Pharma combines the Group-wide activities of Van Hessen, Devro and Bioiberica in the field of natural casings, collagen-based edible films and coatings, as well as and pharmaceutical active ingredients. Check out the latest trending topics regarding this division by clicking on the red button below.
The topics are: Employee survey by Van Hessen // Van Hessen at Anuga 2023 // Devro celebrates Safety Month // Bioiberica at the CPHI
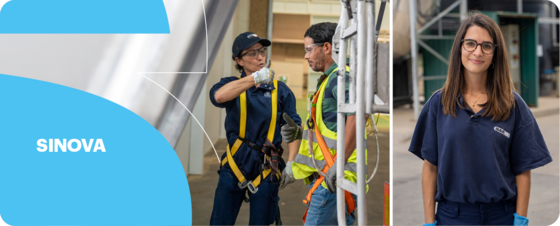
Sinova combines the Group-wide activities of SARVAL and Bioceval in the field of animal feed industry, oleochemistry and agriculture. Check out the latest trending topics regarding this division by clicking on the red button below.
The topics are: Sinova: ‘O’ for Oleochemicals // Close to action – Sinova Townhall Meetings
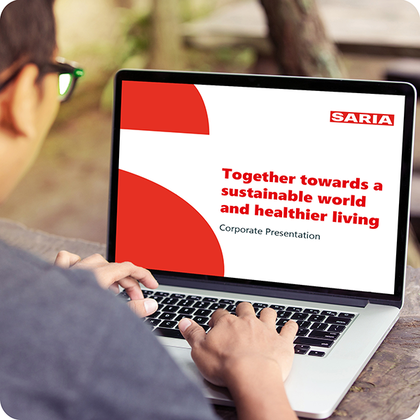
New SARIA Corporate Presentation
In search for a great overview of our activities and key facts? Check out the updated power point presentation in our new corporate design! You can also find access to the SARIA Brand Book and the new SARIA power point master.
Use this for your internal and external presentation of our SARIA Group!
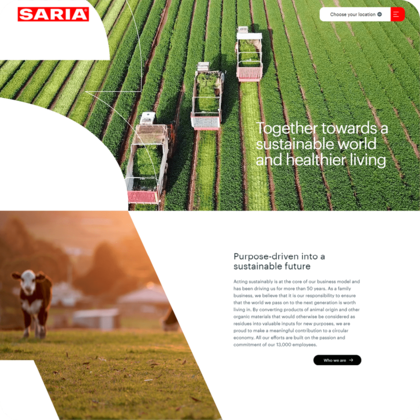
New global
SARIA website
The global SARIA website shines in the new corporate design. In addition to the individual SARIA country websites, this website is intended to be our international, Group-wide flagship for external presentation.
Discover new content and learn more about who we are and what we do!
EcoVadis Medal 2023
SARIA Group has been awarded the silver medal by EcoVadis, the global standard for business sustainability ratings.
Our current score places us in the top 7 % of all companies evaluated worldwide. SARIA has completed this comprehensive assessment every year since 2016 and was able to steadily improve its Group-wide rating.

Changes in the responsibilities of SARIA UK business
At the end of 2023 there will be changes in the responsibilities for the SARIA UK activities at SARIA Executive Board level.
Dr. Peter Hill will take on the responsibility for the SARIA UK businesses. Franz-Bernhard Thier will remain responsible for ReFood UK Ltd and T.Quality Ltd, including Nortech Foods Ltd. In addition, the successive integration of the UK Finance & Administration functions into the Group Functions led by Tim Schwencke will be started.
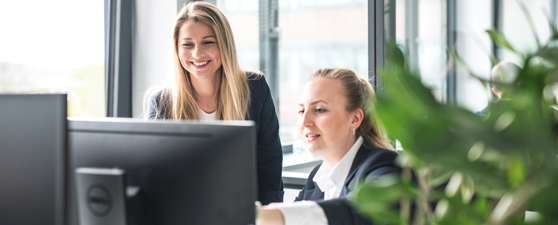
What comes next?
You can look forward to the next SARIA Global Newsletter in 2024.
You have ideas, wishes, comments? Share them with us at: newsletter@saria.com.
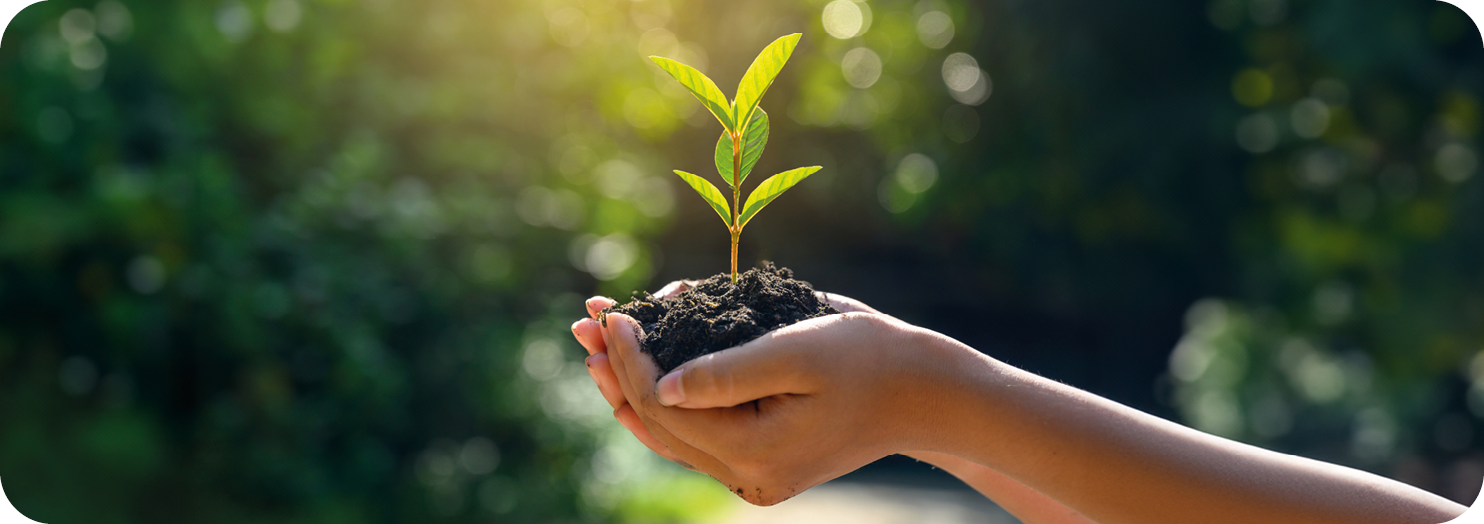
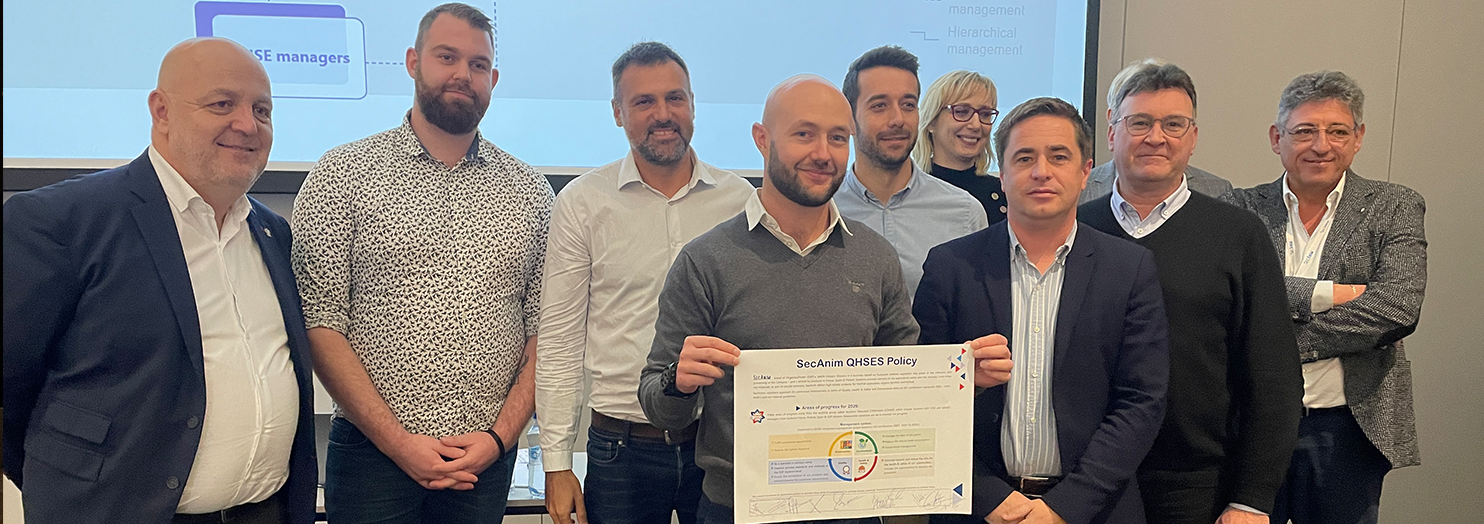
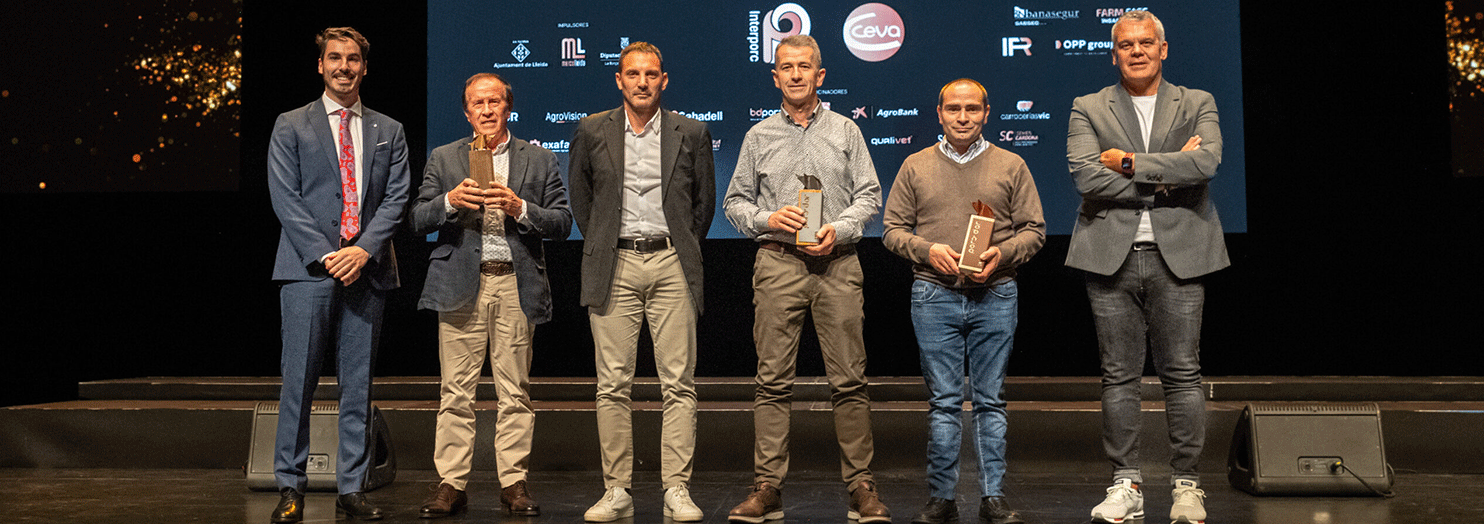
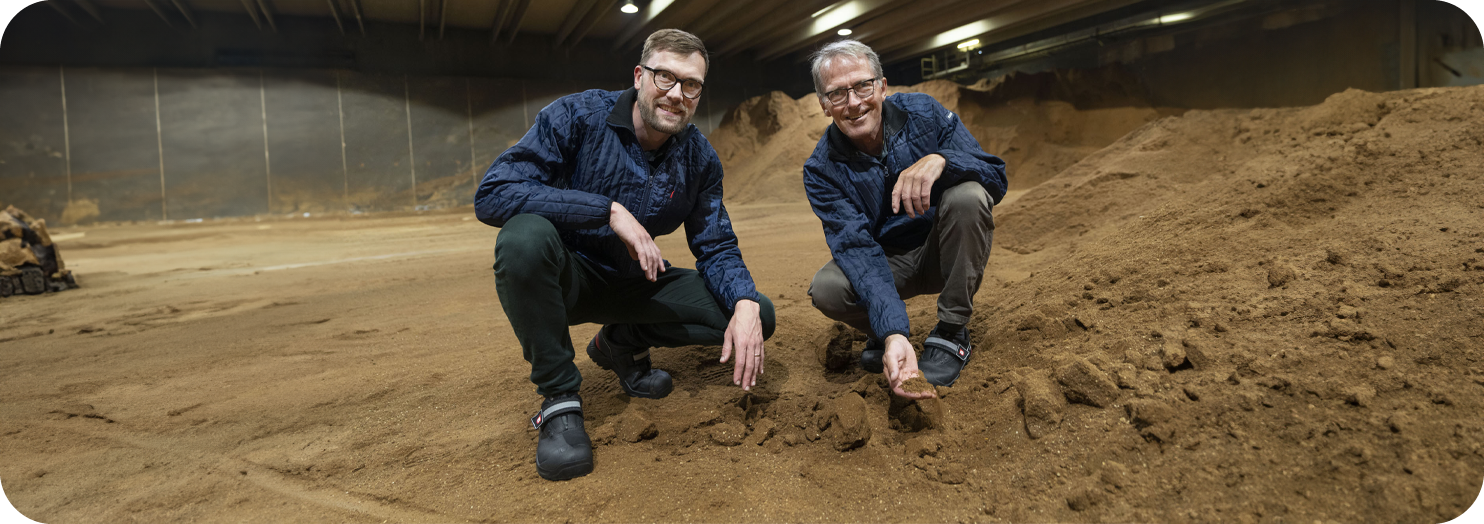
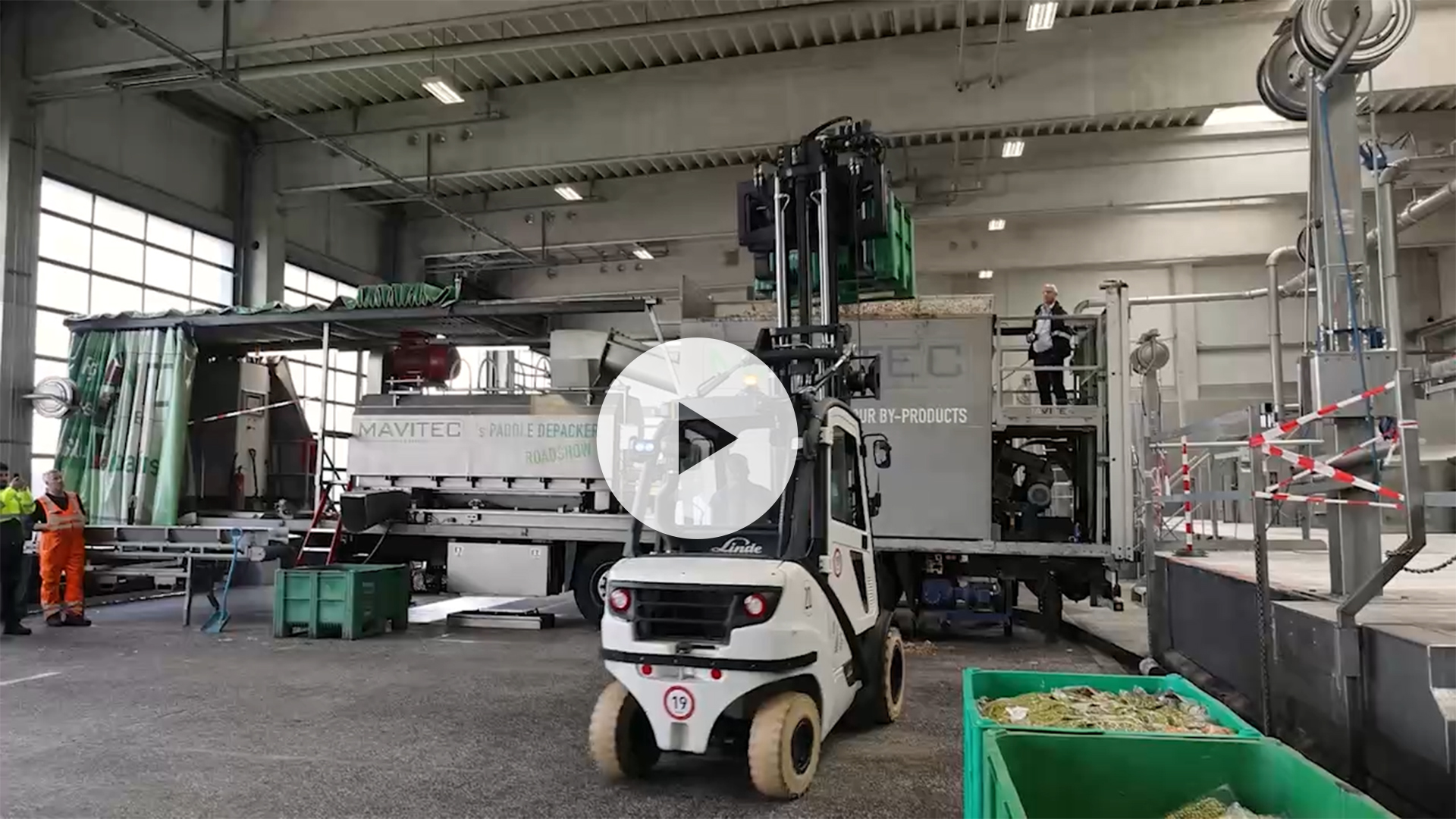
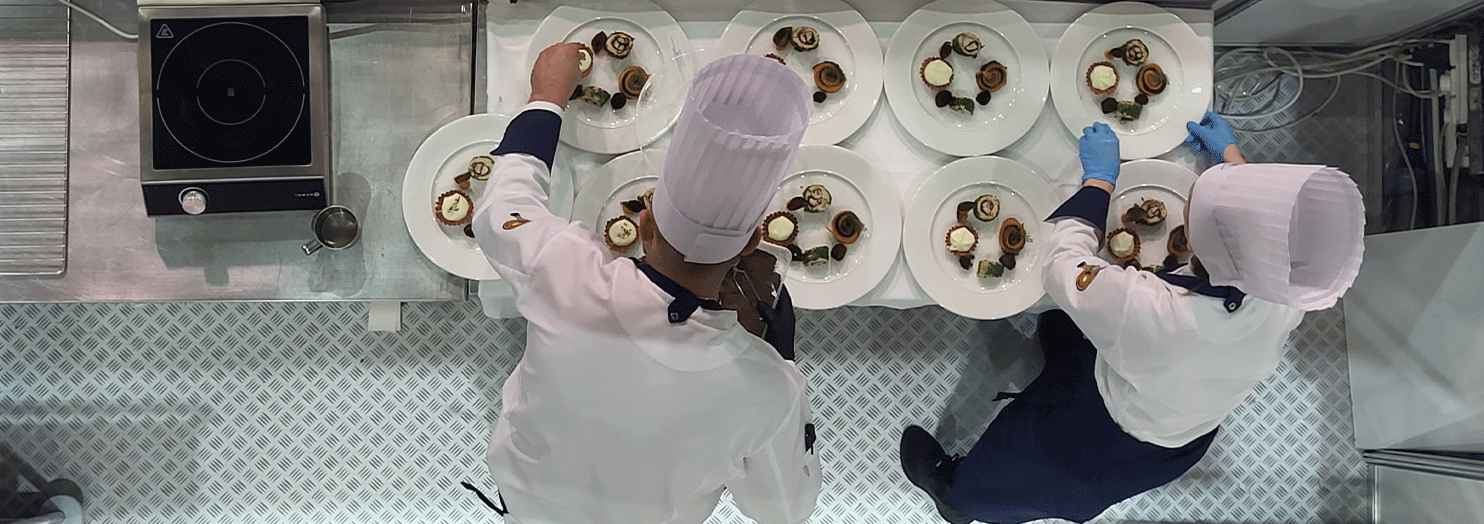
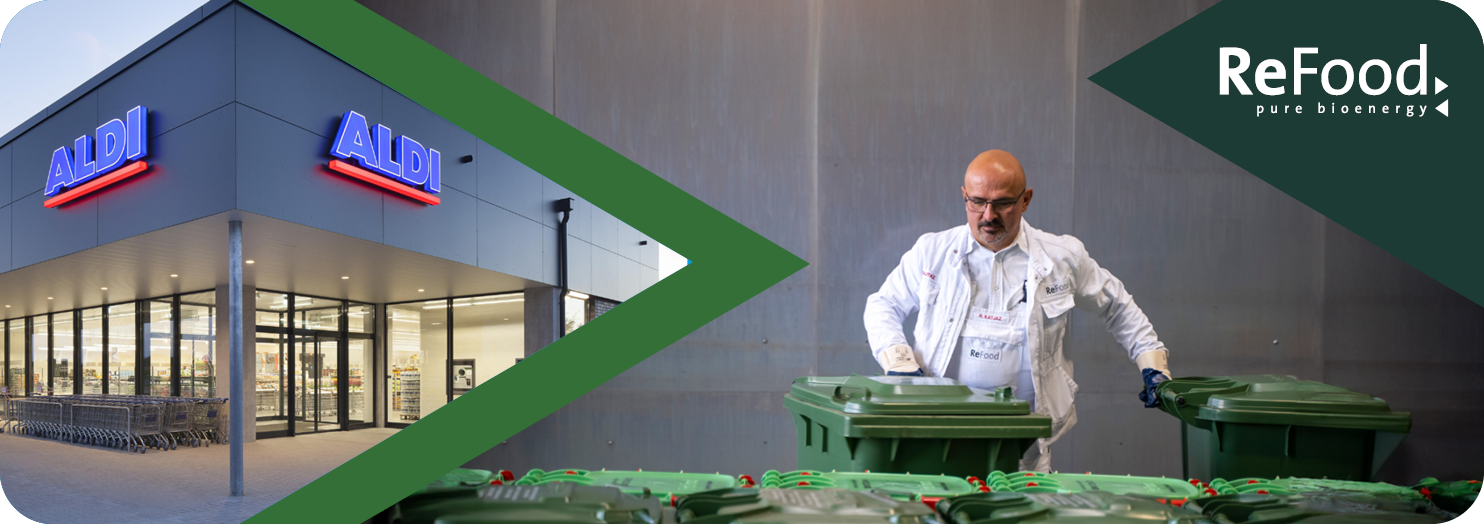

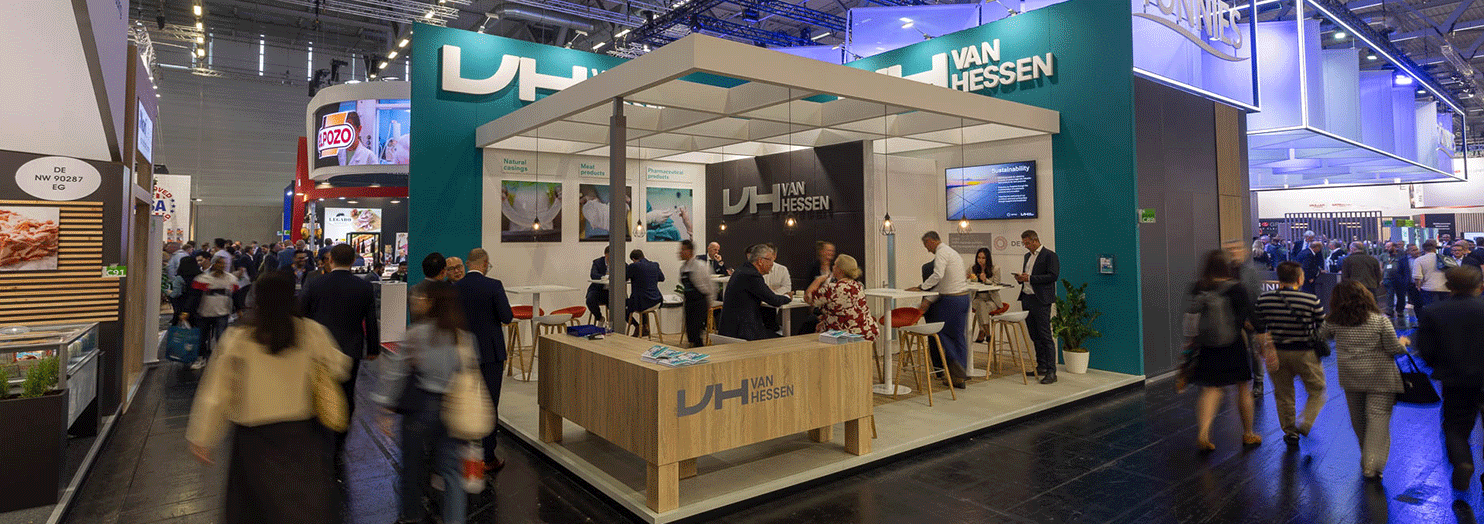
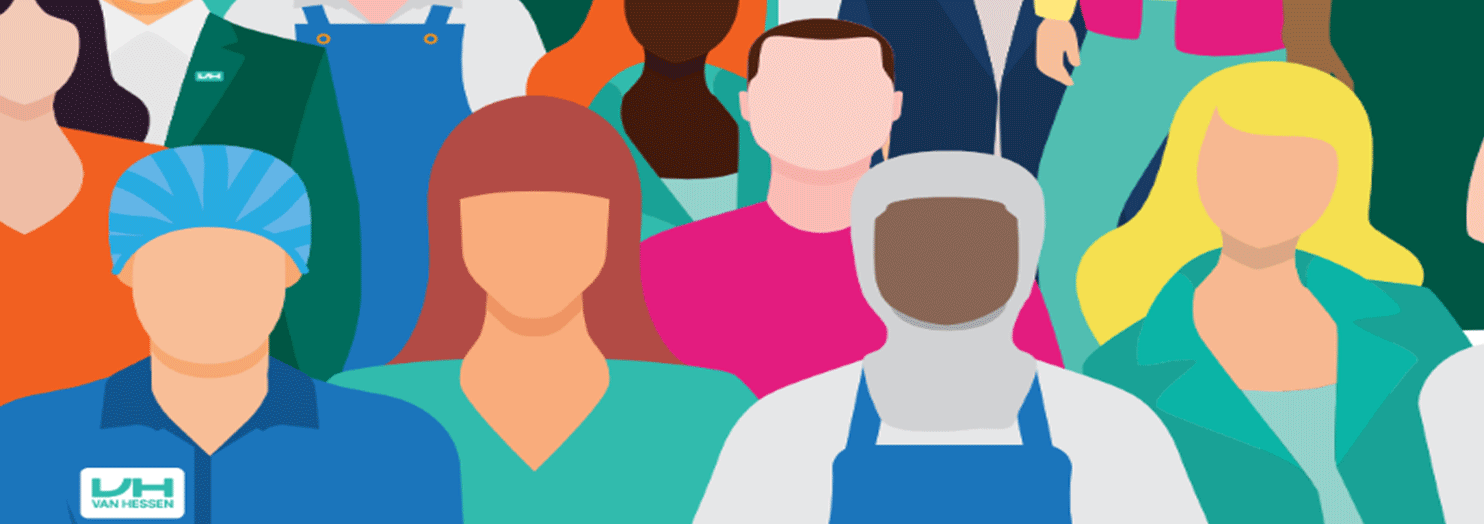
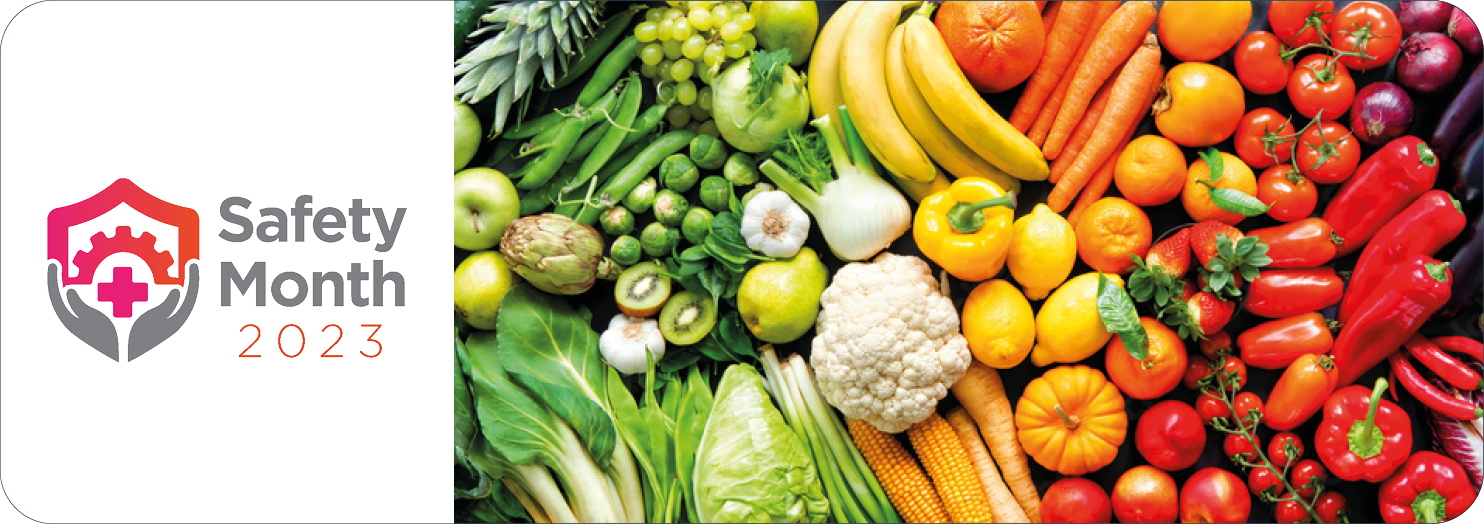
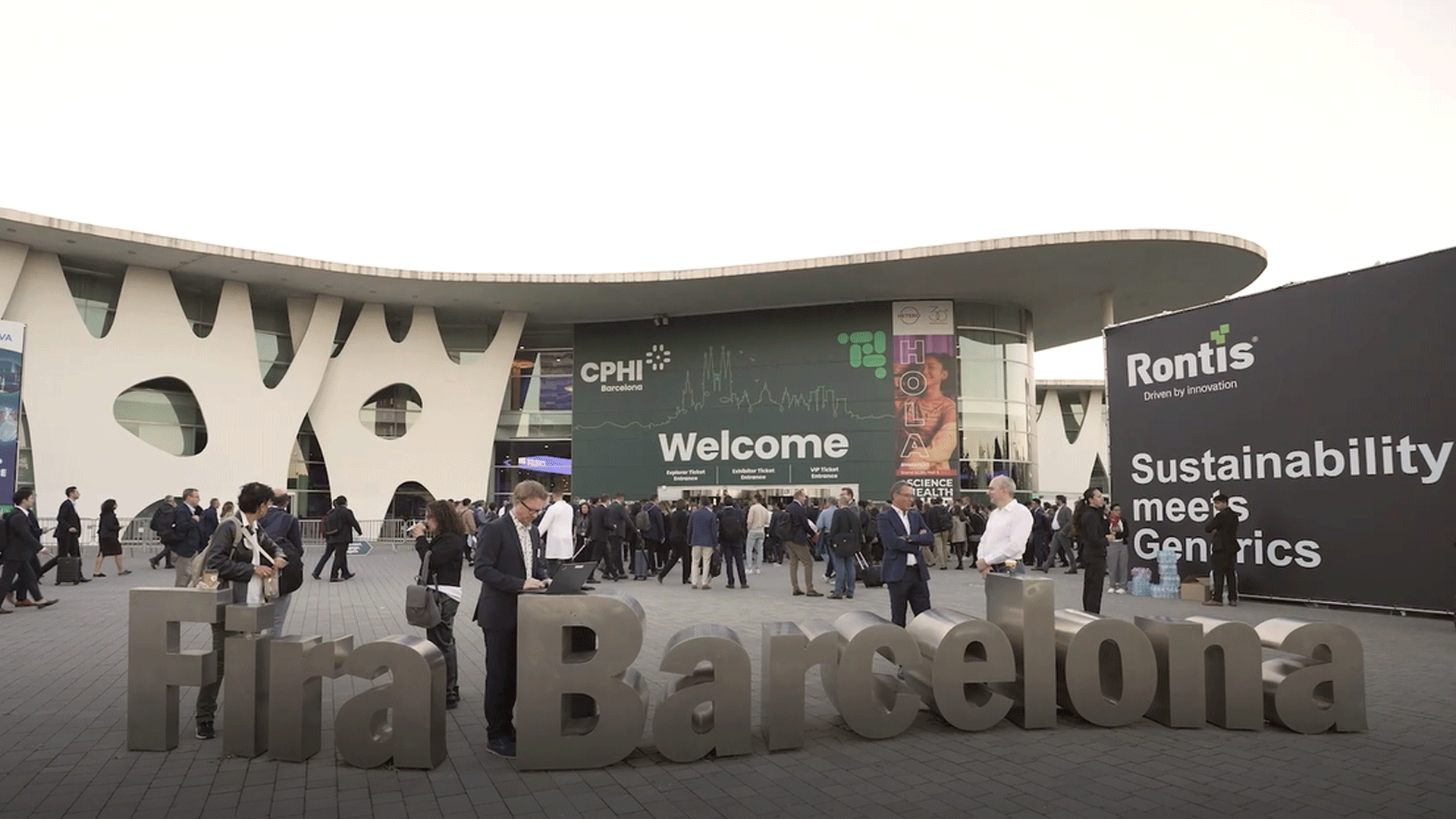
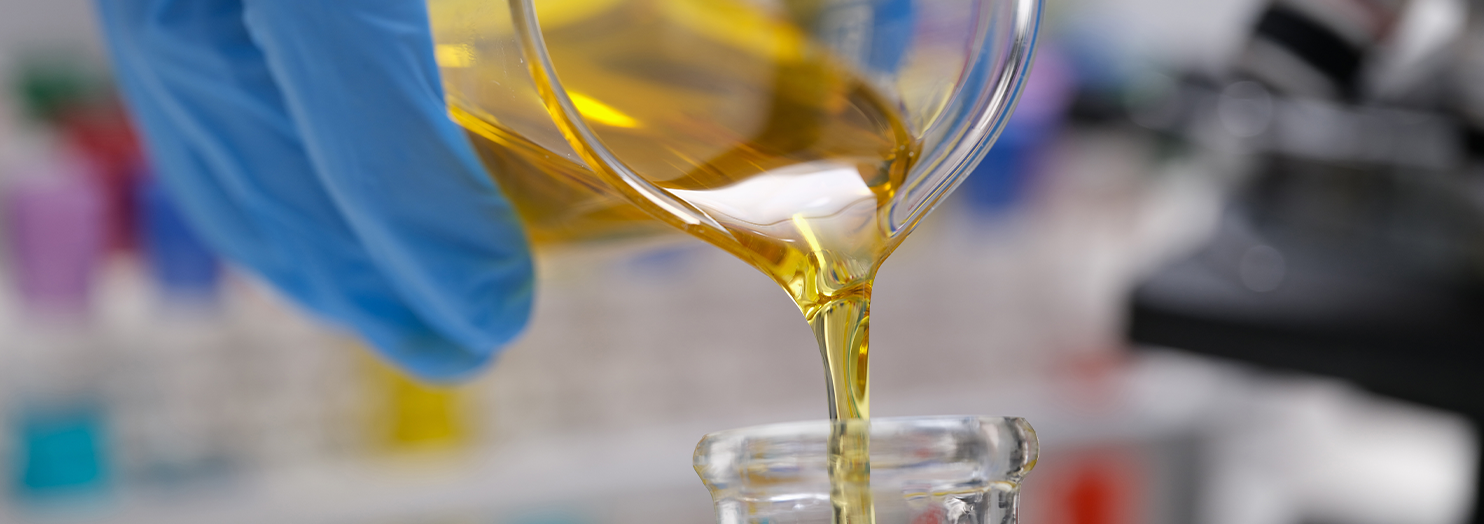
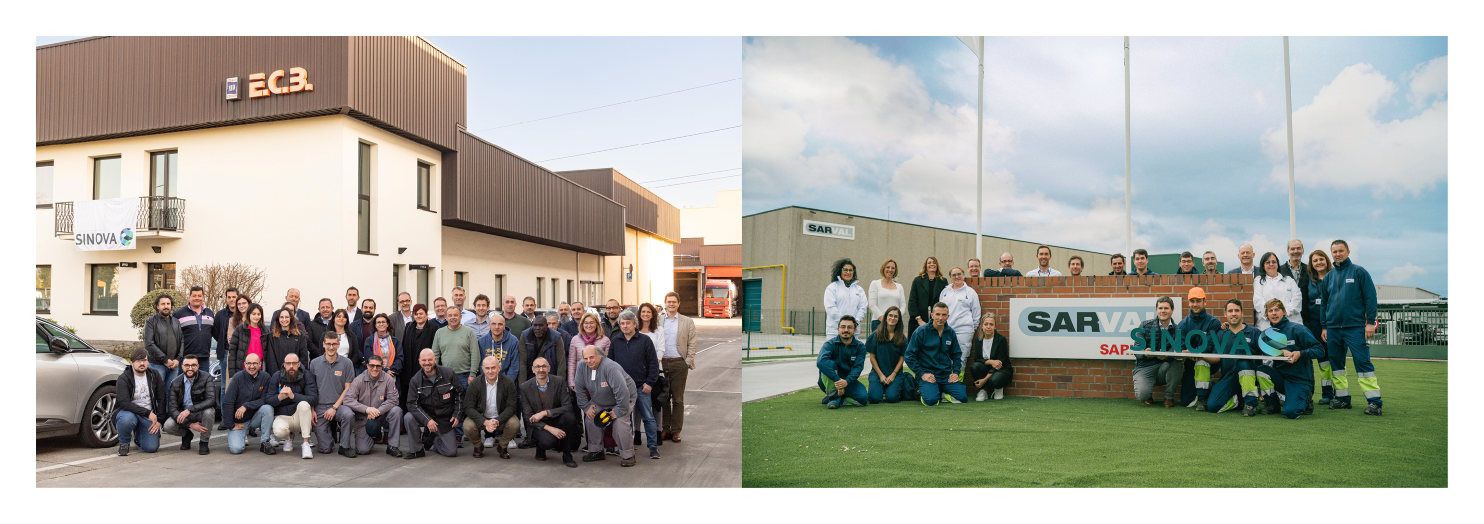
No. 04/2023
Organics2Power: certification of our first net CO2 Fertilizer
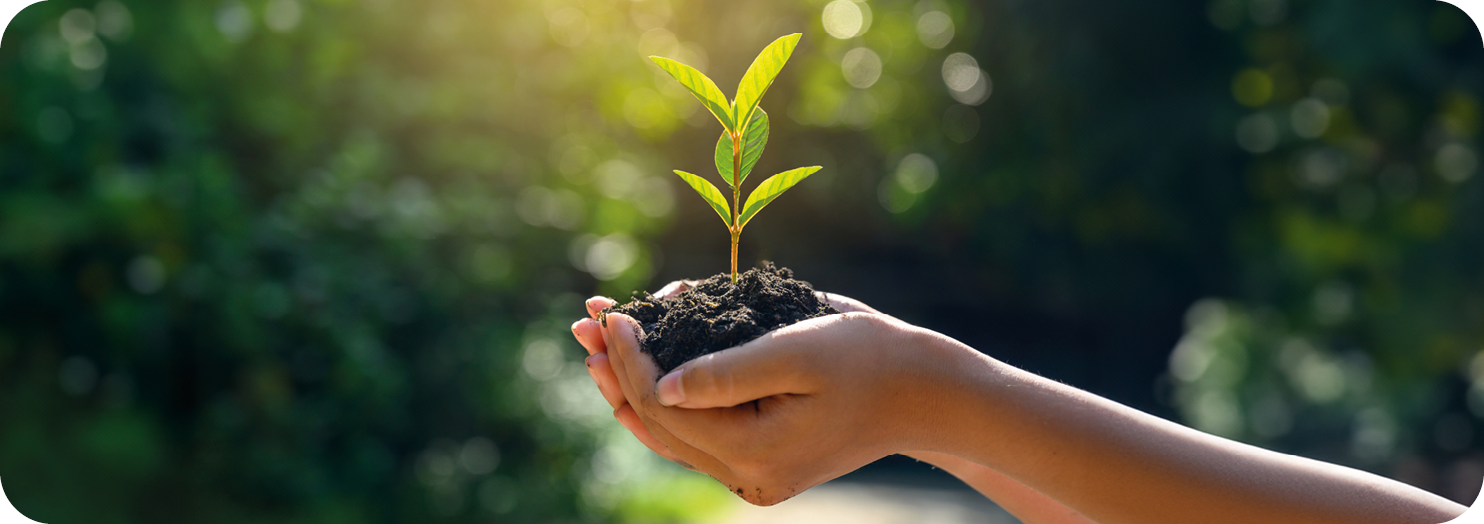
In a world increasingly concerned about sustainability and environmental impact, companies are challenged to find innovative solutions to reduce their carbon footprint.
The Organics2Power Division is proud to announce an exciting breakthrough that marks a milestone in our commitment to environmental responsibility: the certification of our first zero carbon footprint fertilizer. This achievement represents a significant step towards reducing our Product Carbon Footprint (PCF) and ultimately our Corporate Carbon Footprint (CCF).
Why is the certification of a Net Zero CO2 fertilizer important?
Before delving into the details of this achievement, it is important to understand the importance of a Net Zero CO2 fertilizer. Agriculture, a vital sector for human survival, is a significant source of greenhouse gas emissions. The production of traditional fertilizers is also CO2 intensive. Therefore, the creation and certification of a carbon neutral fertilizer is a critical step in addressing climate change and moving towards a more sustainable agriculture.
The certification process
Over the past few months, the Organics2Power sustainability team, led by Roberto Perez, has been working tirelessly to develop and certify one of our two fertilizers.
This process involved a careful assessment of all stages of production and distribution, from raw material to field application. Each stage was analyzed for opportunities to reduce carbon emissions, and those that could not be reduced were offset through voluntary Gold Standard carbon credits.
As can be seen in the graph, Dynasol+, our category 2 fertilizer produced by SecAnim, has zero carbon emissions compared to other products on the market.
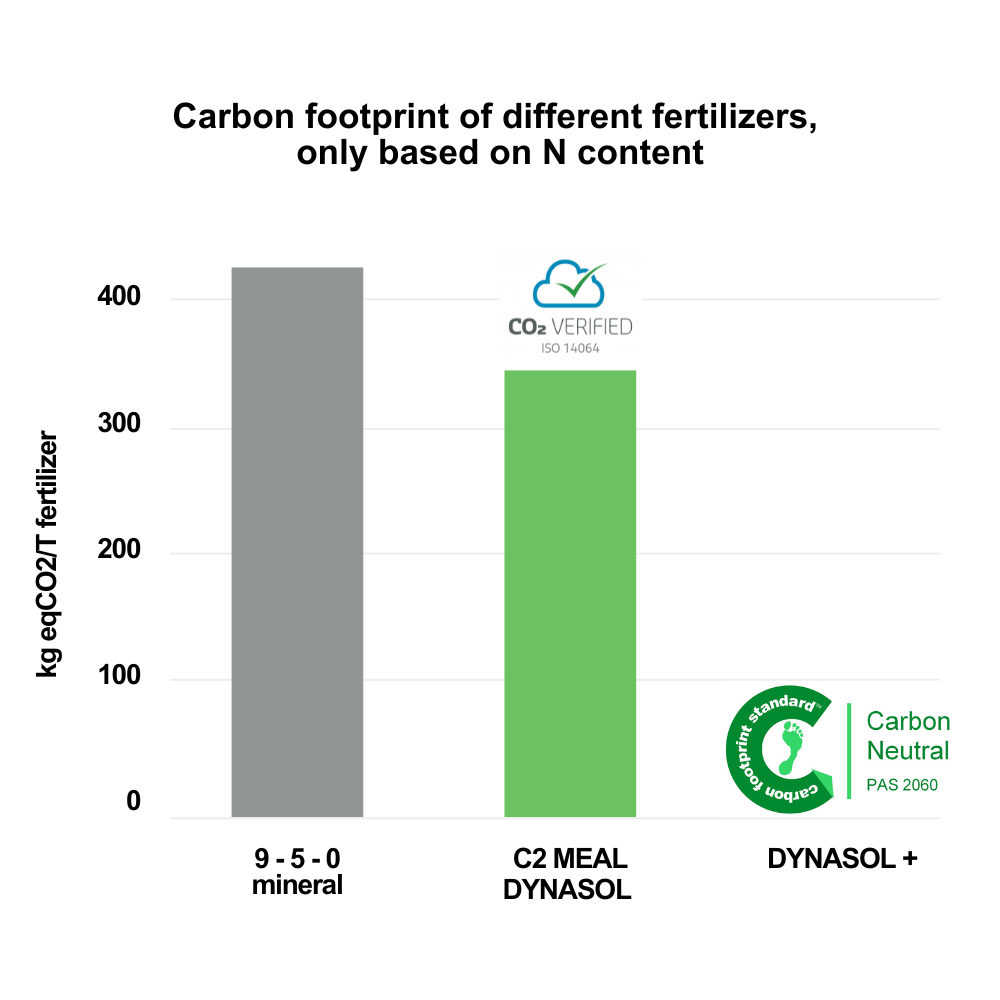
Benefits for the company and the environment
The certification of our first Net Zero CO2 fertilizer has significant benefits for the Organics2Power Division and the environment as a whole. Firstly, it strengthens our position as a leader in sustainability, which can attract consumers and business partners who are committed to reducing their own carbon footprint. Second, it allows us to increase our competitiveness, which translates into a higher selling price.
In addition, this certification makes a concrete contribution to reducing CO2 emissions in agriculture, a sector that is often overlooked in efforts to combat climate change. By providing farmers with a sustainable alternative, we are helping to address a critical issue.
Leading the way to a more sustainable future
The certification is just the beginning of our commitment to sustainability. At Organics2Power Division, we are committed to continually innovating and improving our practices to reduce our carbon footprint and contribute to the well-being of our planet.
Organics2Power: SecAnim meeting. We are the team.
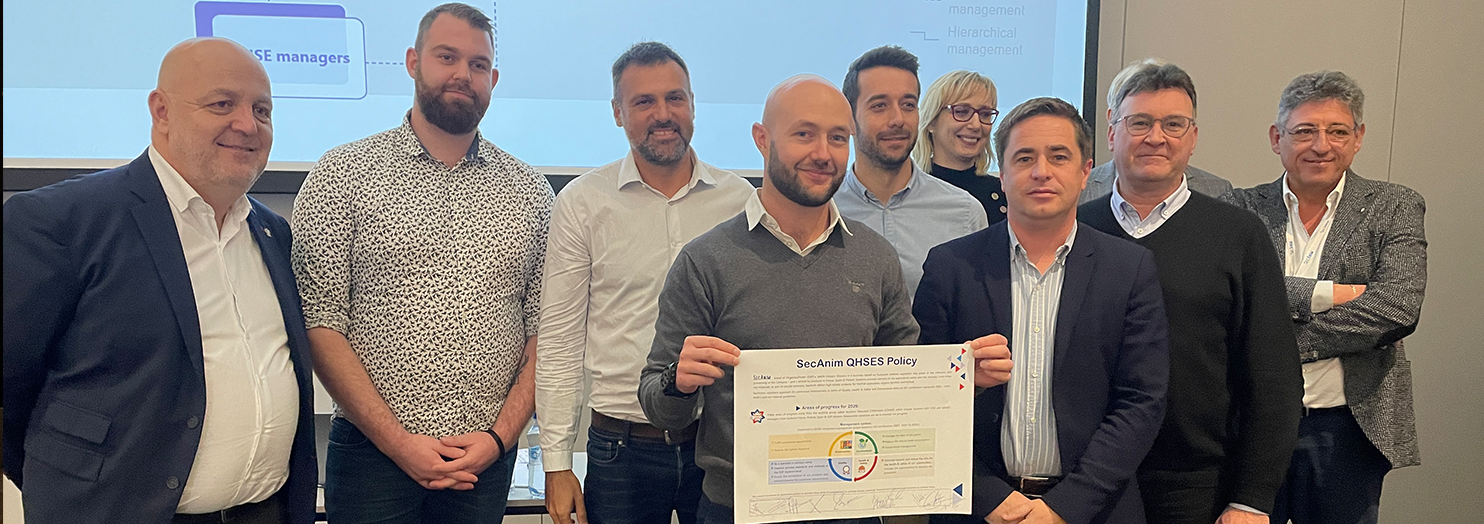
On November 9-10, SecAnim representatives from Poland, France and Spain met in Warsaw. Guests from Germany were also present.
The meeting was attended by SecAnim representatives (divisional and country COOs, plant managers) and O2P division representatives from Logistics, Smart Technology, Finance, Sustainability, Public Relations and Communication.
It should be remembered that the markets in each country where SecAnim operates are organized differently. The regulatory environment is also slightly different, affecting different customer segments. But SecAnim faces the same challenges in each market, such as raw material availability, energy prices and competition. That is why it is so important to benefit from the strength of SecAnim’s international reach. By working together and sharing information and best practices, we are smarter. We create global standards and processes, and we are better prepared to meet future challenges.

The program was very rich. Over the course of two days, participants learned details about the financial situation, forecasts and dependencies that affect CAPEX opportunities. Managers signed the SecAnim QHSES (Quality Health Safety Environmental Sustainability) policy applicable to all countries. Smart Technology also presented innovations in fat recovery options for already produced meals. Participants also had a special workshop to demonstrate the importance of collaboration, information sharing and the use of English.
Communication presented SecAnim’s brand strategy as an international player. It was an excellent opportunity to see what values are at the heart of the SecAnim brand and how we want to position ourselves in the eyes of our customers and other stakeholders. In addition, a special panel discussion was dedicated to the effective collaboration of SecAnim’s logistics and operations. All of this was tied together by building and strengthening our team. During the panel, we used the Mentimeter tool, which allowed us to anonymously measure how the participants received the message and, most importantly, how much they wanted to engage in effective collaboration. The results are clear – we are the team with a common goal.
SecAnim Spain: boosting the pig sector through sponsorship of the Porc d’Or Awards
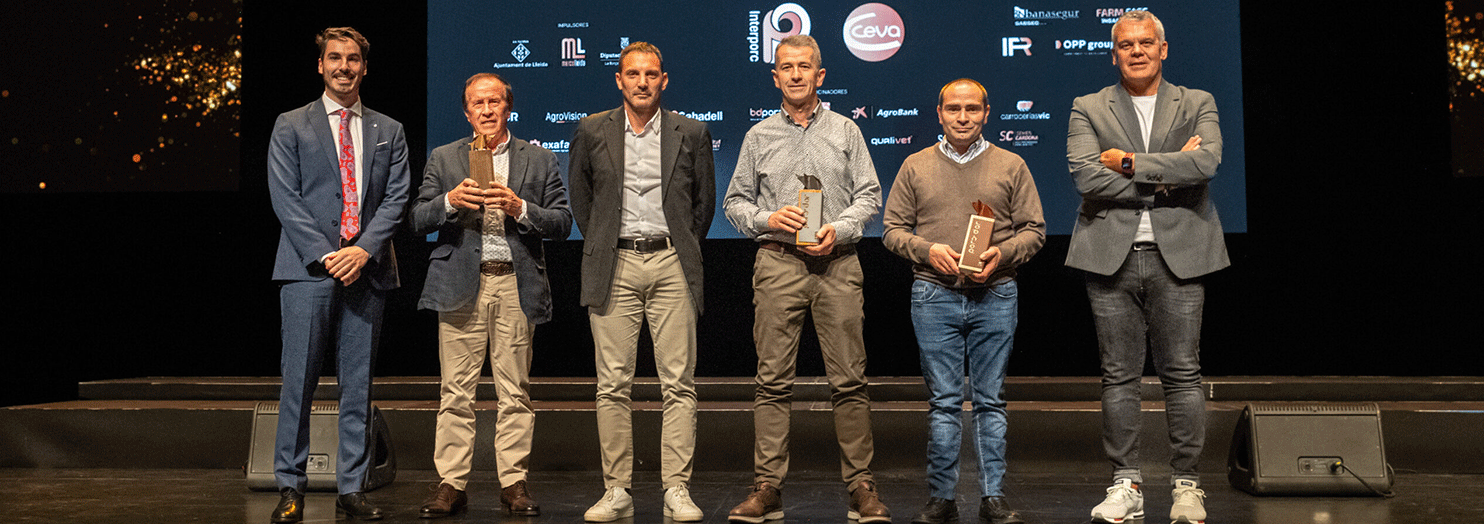
The pig sector in Spain is a vital industry that plays a fundamental role in the country’s economy.
With more than 900 participants, including farmers, veterinarians, representatives of public administrations, associations, universities and companies, the Porc d’Or Awards have become the benchmark event for this sector. In this context, SecAnim has confirmed its commitment and support for the pork sector by becoming one of the sponsors of these prestigious awards, as it did last year.
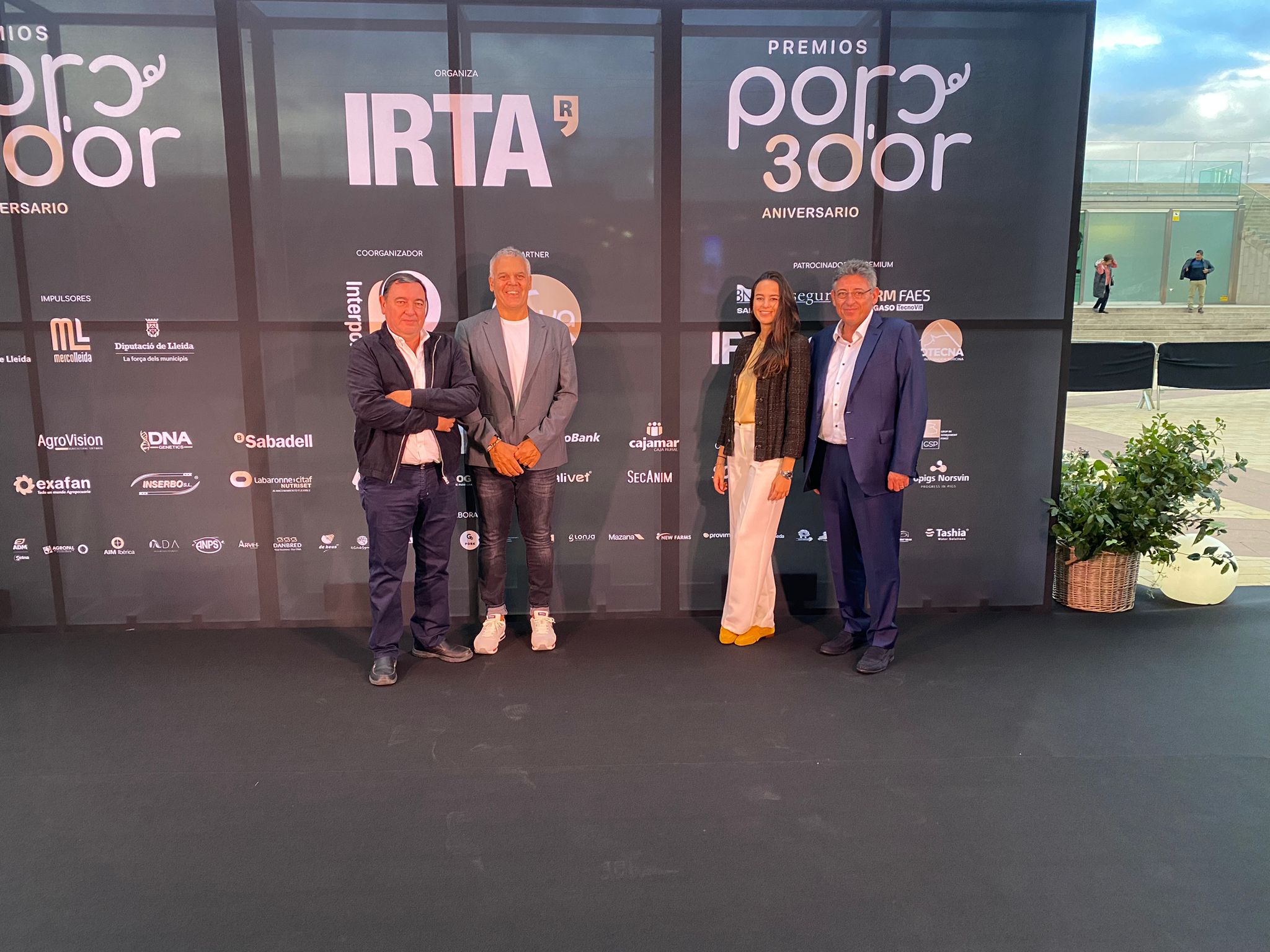
The Porc d’Or Awards are an initiative promoted by the Institute of Agri-Food Research and Technology (IRTA) to recognize excellence in the Spanish pig sector. This annual event highlights the importance of professionalism, effort and daily work in pig farms in Spain, elements that are fundamental to ensure the future of the sector. The values promoted by these awards are fully in line with SecAnim’s philosophy and commitment to Spanish farmers.
In the 30th edition of the Porc d’Or Awards, held in Lleida (Spain) on October 20th, SecAnim was present as one of the sponsors of the event. The company’s participation in these awards demonstrates its active support for the pig sector and its commitment to recognizing excellence in the industry.
Miquel Vila and Laura López, representatives of SecAnim’s management, Miquel Àngel Ausió, commercial manager, and Eduardo Puigvert, sales and purchasing manager, represented the company at the event. Together they had the honor of presenting the Porc d’Or Award in the “Longevity” category, which went to the Pontós farm from Girona (Catalonia). The Porc d’Or Longevity Award has become a prestigious award within the industry and its aim is to celebrate and highlight pig farms that have managed to keep their pigs in optimal conditions for an exceptionally long period of time. This award not only recognizes the producers’ dedication and attention to detail, but also promotes best practices in animal care.
This collaboration not only strengthens SecAnim’s position in the industry, but also demonstrates its commitment to the success and welfare of the country’s farmers and pig farms. The company remains committed to innovation and sustainability in the industry, working hand in hand with its partners to build a more sustainable future for all.
Daka at the “Open Agricultural Day”: more than 150 guests visited
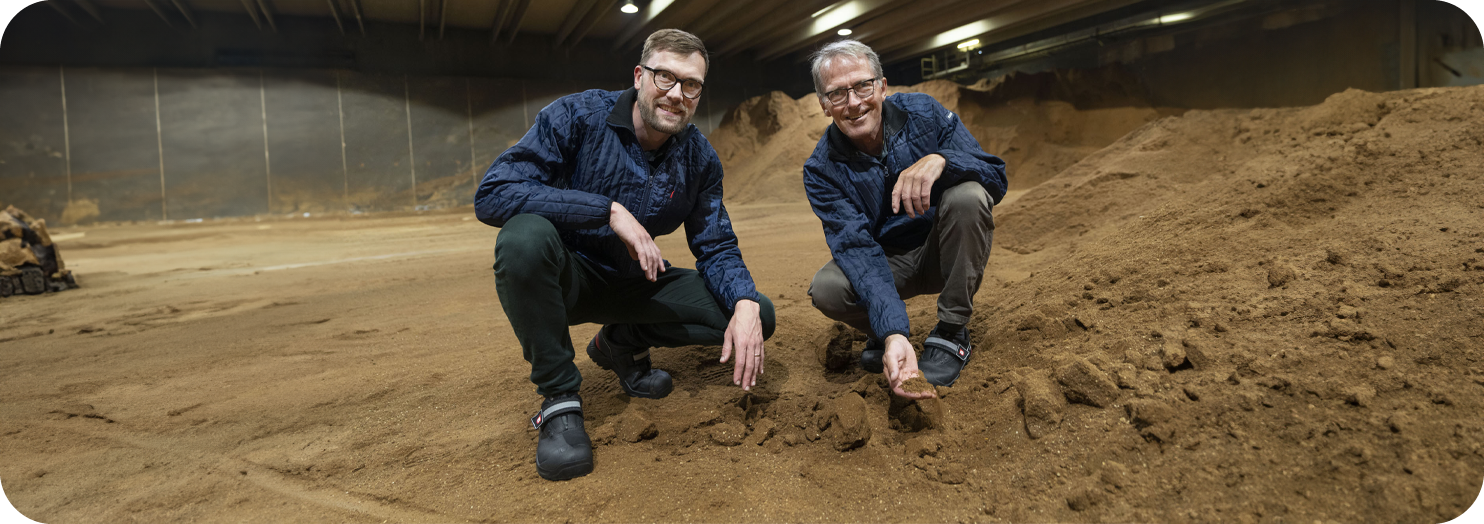
As part of the ongoing development of Daka’s open approach to stakeholders, offering guided tours at the plants, Daka’s participation in the national event Åbent Landbrug (Open Agricultural Day) on September 17, 2023, marked an important milestone for the Daka SecAnim plant in Randers.
The concept, which promotes cooperation between more than 200 farms and agricultural businesses, involves an yearly event where the public is offered an exclusive opportunity for those interested in Danish agriculture to experience it up close.

One of the highlights of the day were the guided tours of Daka’s Randers facility, where guests had the opportunity to observe, ask questions and gain insight into the process of recycling deceased animals from Danish farms into valuable products.
The turnout was impressive, with around 150 visitors taking part in six tours throughout the day. The interest in Daka’s operations was palpable, accompanied by enthusiasm and curiosity.
Feedback from the guests was generally positive, with many expressing a change in perspective and dispelling preconceived notions. Visitors praised Daka’s important role in agriculture and were particularly impressed by the cleanliness and efficiency of the factory.
ReFood Germany: prepares for legislative change
To prepare for an upcoming legal requirement regarding the handling of organic waste in Germany, the ReFood site in Erftstadt (Germany) tested the large version of the Mavitec Paddle Depacker – a machine used to separate packaging and organic material.
Legislative reform
To reduce the proliferation of micro plastic into the environment, new check values for plastic in organic waste have been adopted in the Biowaste Directive, which was passed in Germany in the beginning of 2023. These check values are part of the new Requirements for the removal of external substances and will become effective in Germany on May 1, 2025. The German Biowaste Directive require that processors of organic waste must first separate the packaged from the unpackaged fractions. Before further treatment or recycling, the packaged organic material must be unpacked. Therefore, two separate process steps for packaged and unpackaged organic waste and an additional unpackaging unit are required. The Paddle Depacker tested in Erftstadt can combine the two separate process steps in one. The machine can easily unpack food waste and process wet and dry materials.
The Paddle Depacker @ReFood
The extra small version of the machine is already used at the ReFood site in Trossingen (Germany). The large version with up to 30 m3 per hour capacity is used at the ReFood site in Llerona (Spain) as well at the newest ReFood site in Mszczonów (Poland).
The Paddle Depacker is a highly effective machine to process biowaste and food leftovers. When the material enters the machine, the rotating axle with paddles will smash, not shred, the input. Due to the smashing action and with the help of interchangeable screens, the organic fraction is forced out of the plastic or metal packaging, while the packaging remains mostly intact. This reduces the amount of plastic and metal packaging in the produced biomass.
The results
The test in Germany confirmed that the generated biomass can comply with the check values for plastic as per the German Biowaste Directive. For the processing of packaged food waste, the test confirmed that the Depacker is currently the technology of choice. For the processing of unpackaged food leftovers, further optimization is needed to reduce the amount of organic fibres and water in the discharge fraction (plastic discharge). It is also practical to install additional equipment such as presses or washing machines after the Depacker. Overall, the test in Erftstadt has shown that the Mavitec Paddle Depacker can be an “all-in-one” solution for ReFood Germany.
ReFood Poland: partner of the Polish Culinary Cup 2023 at Polagra
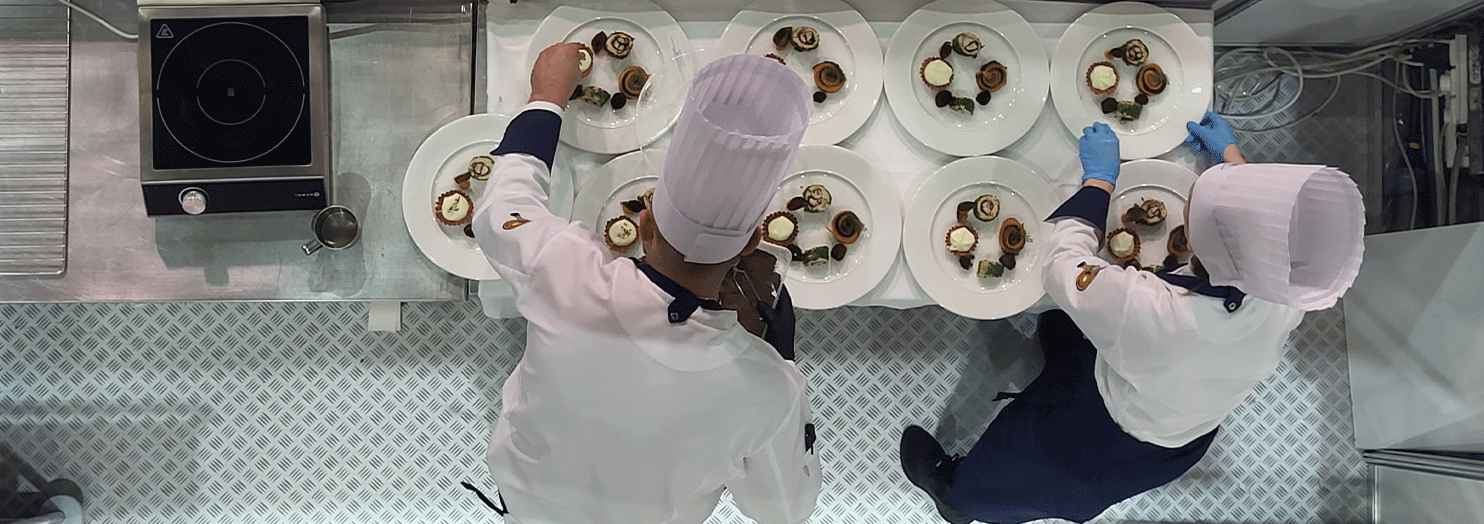
During the intensive two-day competition between the best Polish chefs, ReFood representatives shared their knowledge and experience in the field of food waste management.
We made many valuable contacts, including with outstanding chefs such as Tomasz Purol – winner of the fifth Polish edition of TOP CHEF and Marcin Budynek, founder of the Marcin Budynek Culinary Academy, who is also the official promoter of Polish meat on the international stage.
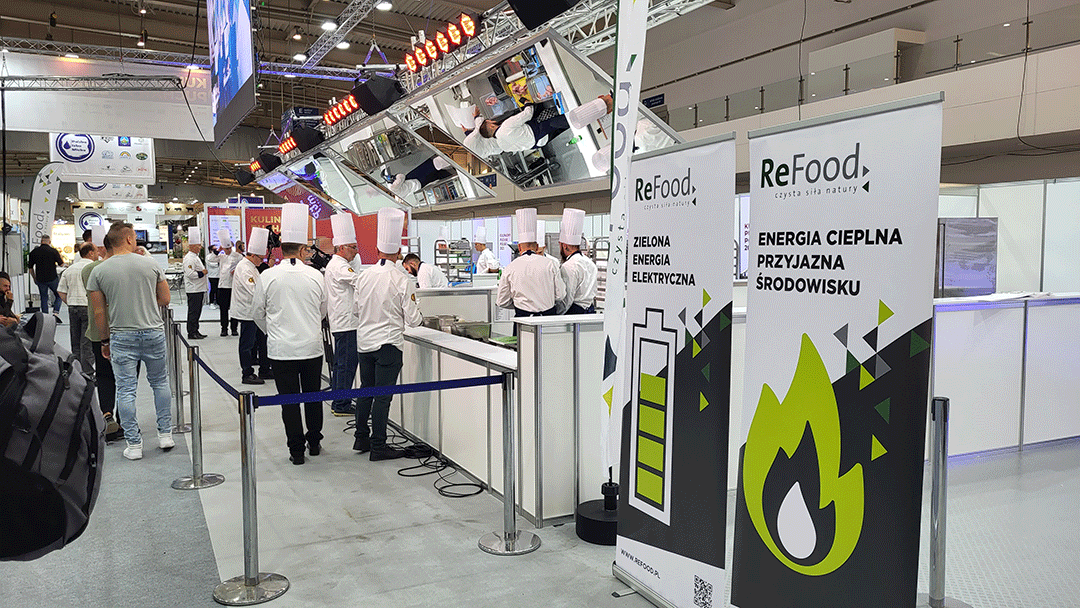
At the fair, we conducted interviews with celebrity chefs, which were broadcast live throughout the fair. In the interviews we focused on the benefits of proper waste management and cooperation with ReFood for restaurants and catering companies. Thanks to us, our HoReCa partners can actively create a circular economy, be part of the green electricity production chain and reduce CO2 emissions.
ReFood Poland: a new client
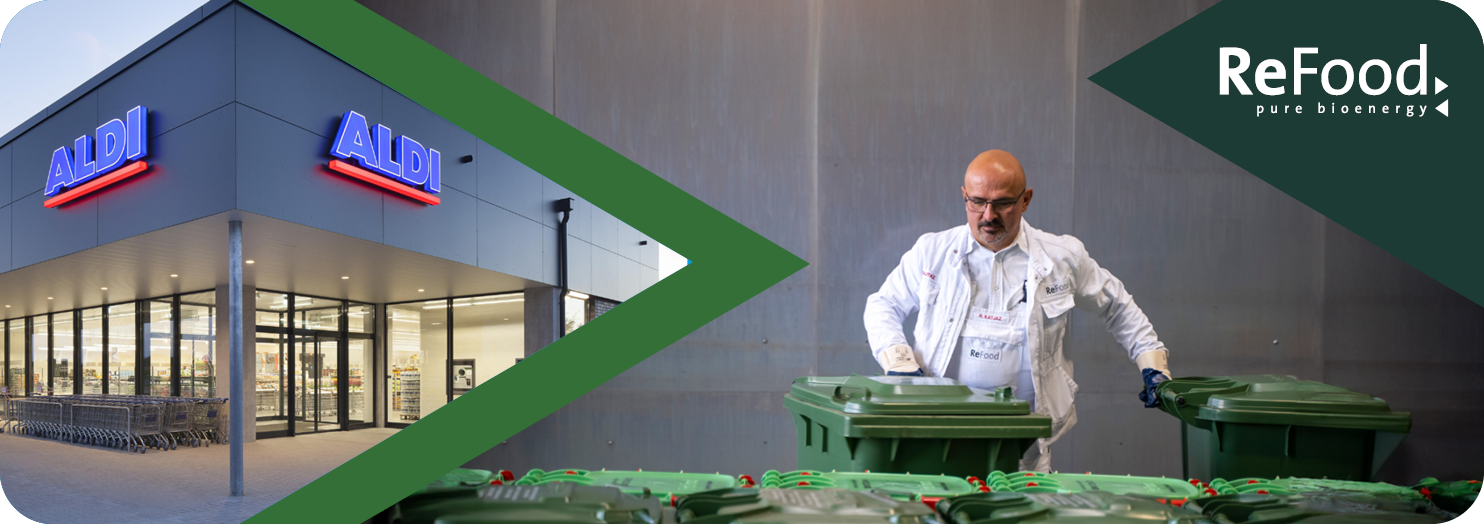
At ReFood, we have taken another big step in the development of our business in Poland.
In September, after long negotiations, we signed a contract with ALDI Polska!
And what does it mean?
As of November 2023, we are ALDI Polska’s exclusive partner for the collection of generated food waste from all 250 supermarkets across Poland.
And that is not all!
Our contract also includes servicing 70 new stores that ALDI plans to open this year! In the long term, ALDI plans to have 600 stores in Poland by the end of 2027 and 1,000 stores by 2032.
ReFood France confirms its position at the Pollutec trade fair

For the first time, the ReFood sales teams are taking part in Pollutec, a key event for expanding the customer portfolio and strengthening ReFood’s presence as a leader in the bio-waste collection and treatment sector.
Pollutec is a major event in France for those concerned with the environment and the ecological and energy transition, bringing together the main players in the sector. This annual event is an excellent opportunity to present ReFood’s solutions to manufacturers, local authorities and other economic players interested in environmental solutions.
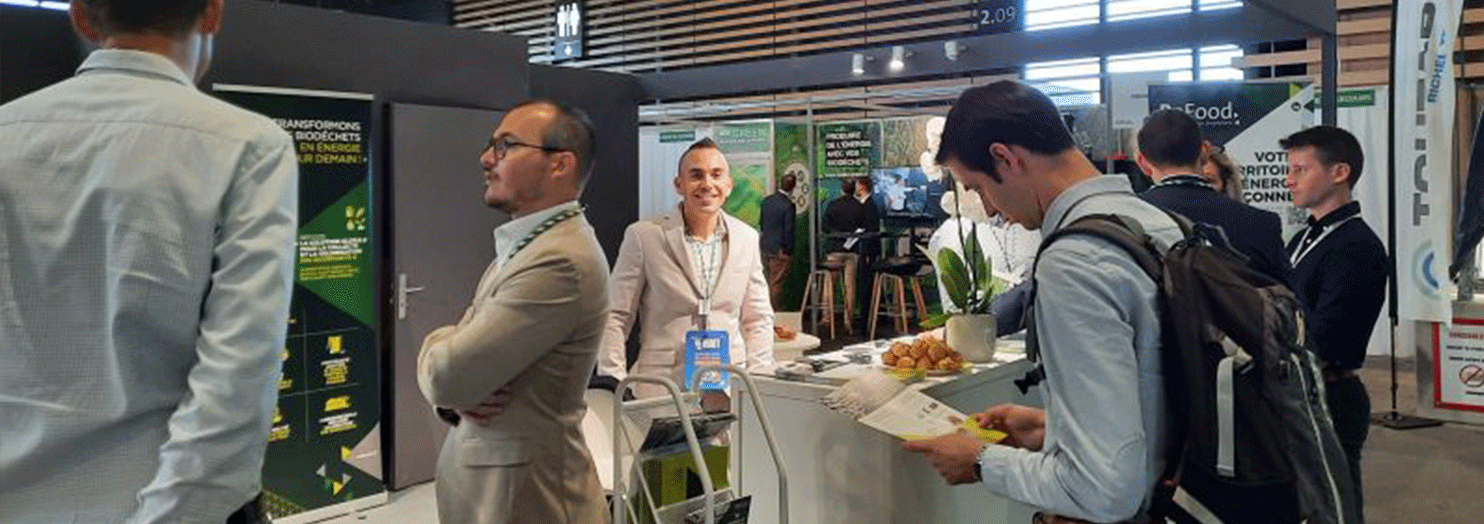
The evolution of the company over the last 10 years, since the creation of the methanization plants, shows that ReFood has acquired a solid legitimacy in the field of bio-waste collection and treatment. What’s more, the fact that the people we talk to are increasingly well informed about the subject is a positive sign, even if there are more competing players on the market. ReFood’s ability to highlight its competitive advantages, such as proximity and collection methods, is an essential asset if it is to compete with major players such as SUEZ or Paprec.
According to Alexandra LE CORPS, market manager for the food industry, “Various players, such as local authorities, the agri-food industry, restaurant chains, independent caterers and partners, came to meet us on our stand because they are now familiar with our expertise. We have the feeling that the market is more mature and that producers or holders of organic matter are open to discovering new partners for the management of their bio-waste, something they didn’t do a few years ago. We now have our full place at Pollutec.”
It is also important to note that the success of the exchanges at Pollutec is the result of understanding visitors’ expectations.
All in all, ReFood seems to be well positioned to capitalize on the success of its participation at Pollutec by continuing to present its offer to players in the environmental sector and the ecological transition.
So, see you next year at Pollutec 2024?
Recap Van Hessen at Anuga 2023
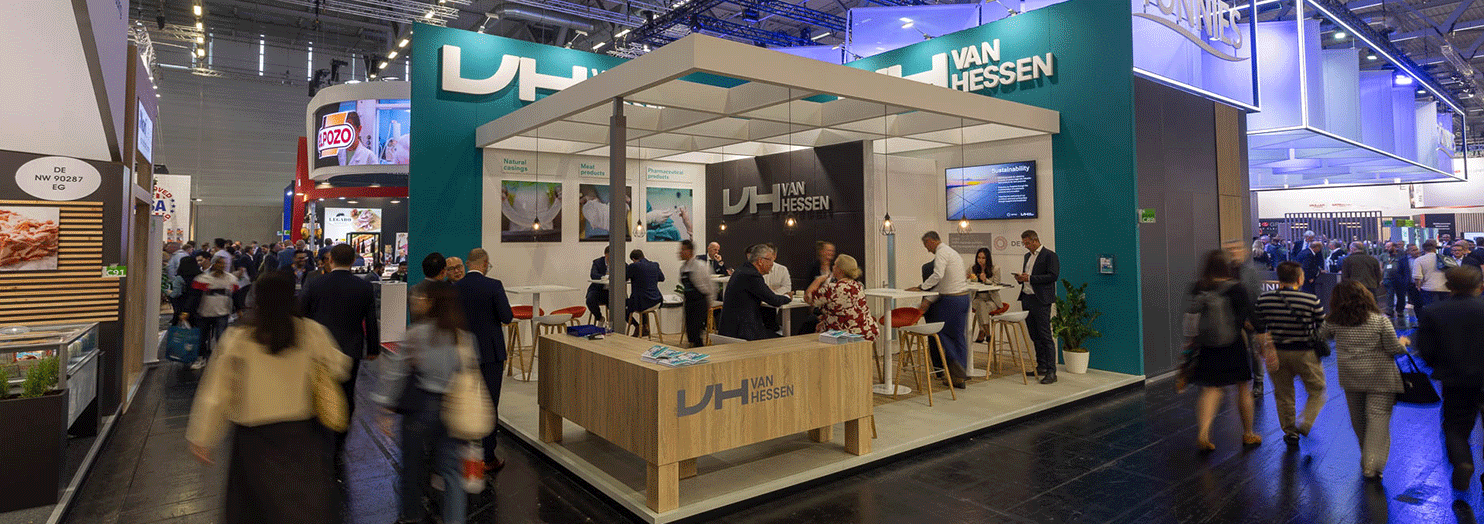
From October 7 to 11, 2023, the Anuga Fair in Cologne took place and, as usual, Van Hessen welcomed suppliers and customers from all over the world to its booth.
Unlike previous years, this year we had the pleasure of attending together with representatives of our new sister company Devro.
Many of our customers made their way to our booth to talk with our colleagues. We told them more about the benefits of being able to provide both natural and collagen casings and the common values between Van Hessen and Devro. The booth was constantly busy and on Monday evening we had a joint company meal to get to know each other better.
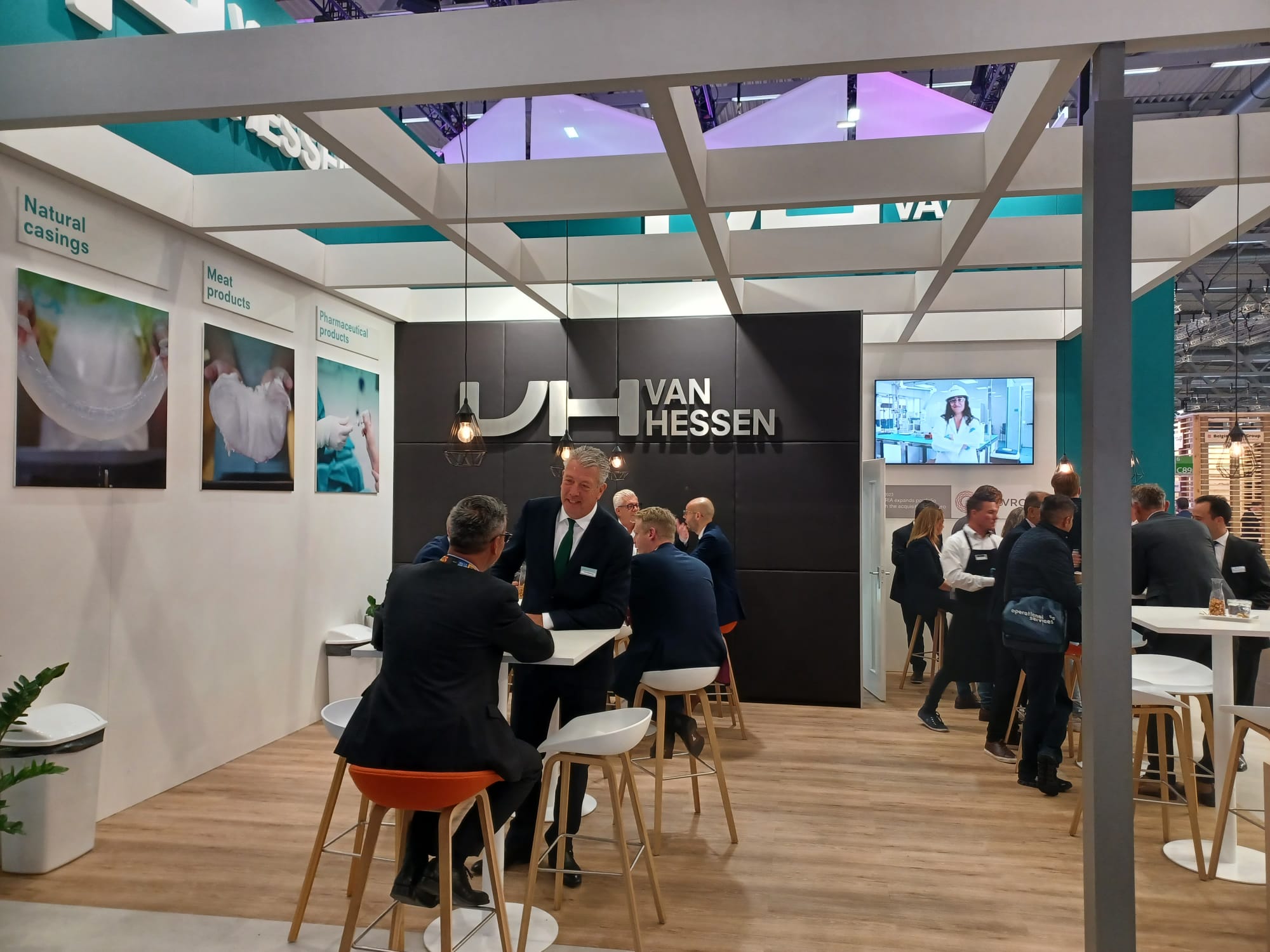
Anuga allows exhibitors and trade visitors to experience the diversity of the food and beverage industry in 10 trade shows under one roof. In every specialist segment, each food trade fair is unique and presents products and services related to the respective segment. Many of our business partners and key customers exhibited at the event.
Van Hessen Employee Survey 2023
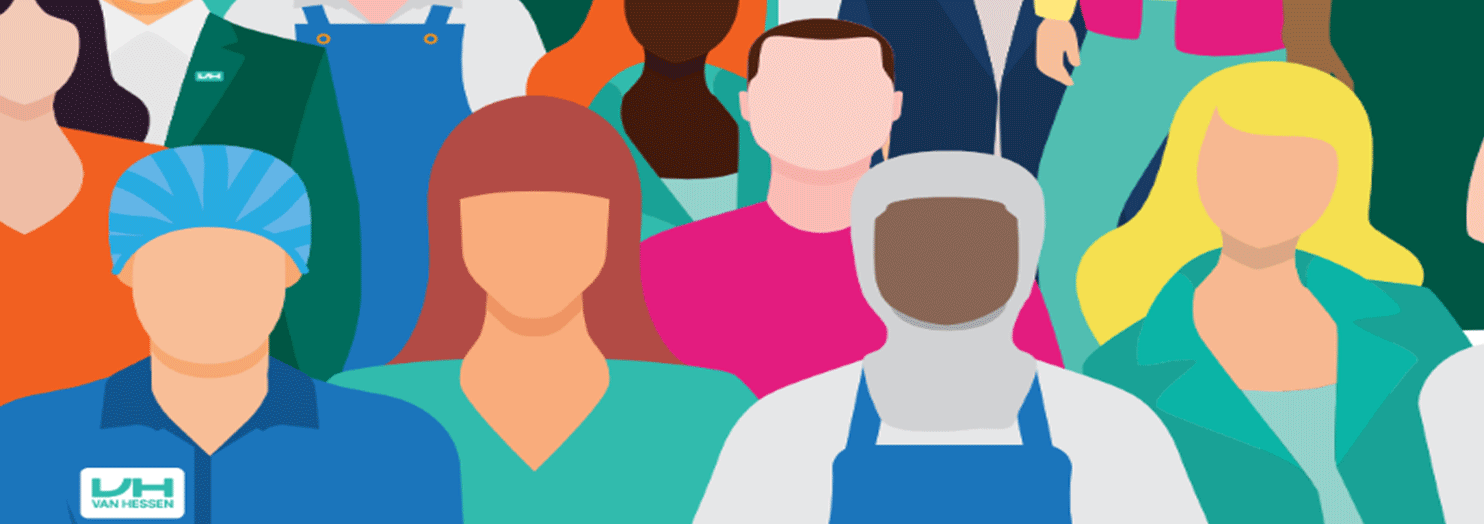
In 2022, Van Hessen conducted an employee survey in the Netherlands with the aim of measuring and enhancing employees’ work experience.
Based on the results, everyone has worked diligently over the past year on improvements to ensure that employees in the Netherlands have an even more pleasant experience working at Van Hessen.
The employee survey was further rolled out globally in 2023. All employees on the payroll at Van Hessen were asked for their opinion. There were a few exceptions: UK, Spain, and groups smaller than 7 employees (due to anonymity) were not included. The results were shared with the Management Teams and department managers of the countries/regions. The department managers shared the results with their employees.
We are pleased with the number of participants in the global survey and the results. An average satisfaction rating of 8,12 is something we can all be proud of! Of course, the results also indicate that improvements can be made. For example, communication from and about the organization and management is an area for improvement, as is the balance between work and private life. These are topics to which Van Hessen will pay extra attention.
The countries not included in the survey now, and groups with employees growing to a minimum of 7 people, will participate in the next round of the survey. Within Food & Pharma, we plan to conduct the employee survey periodically globally in all three business units.
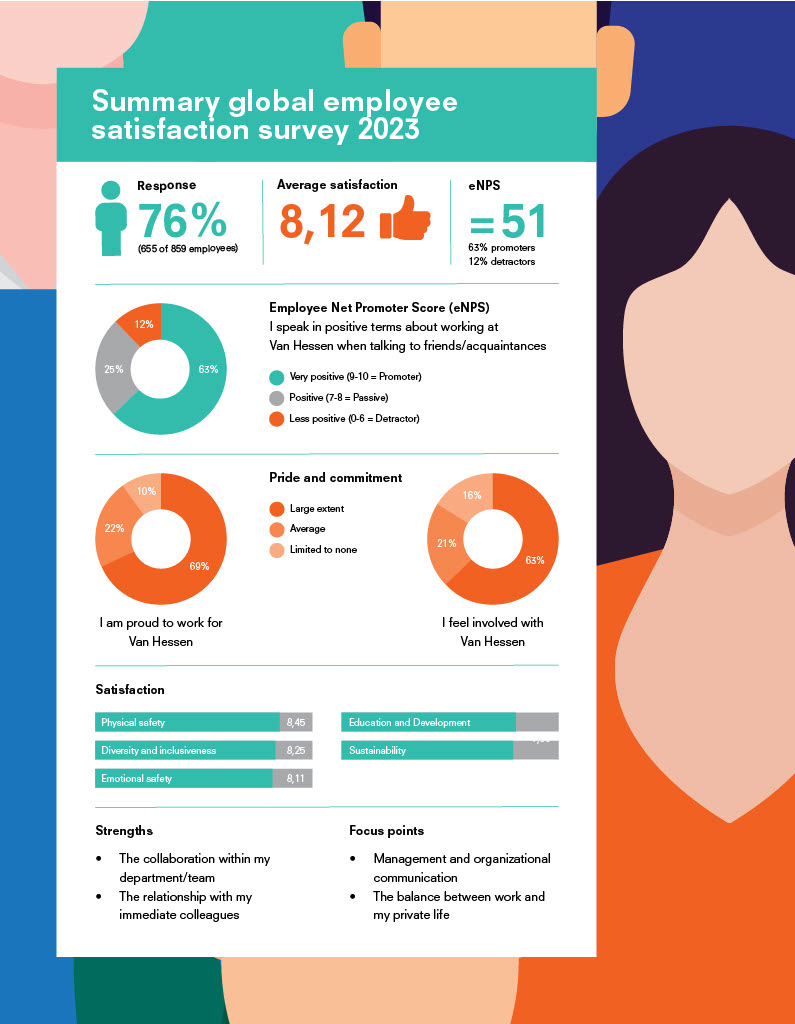
Devro celebrates Safety Month
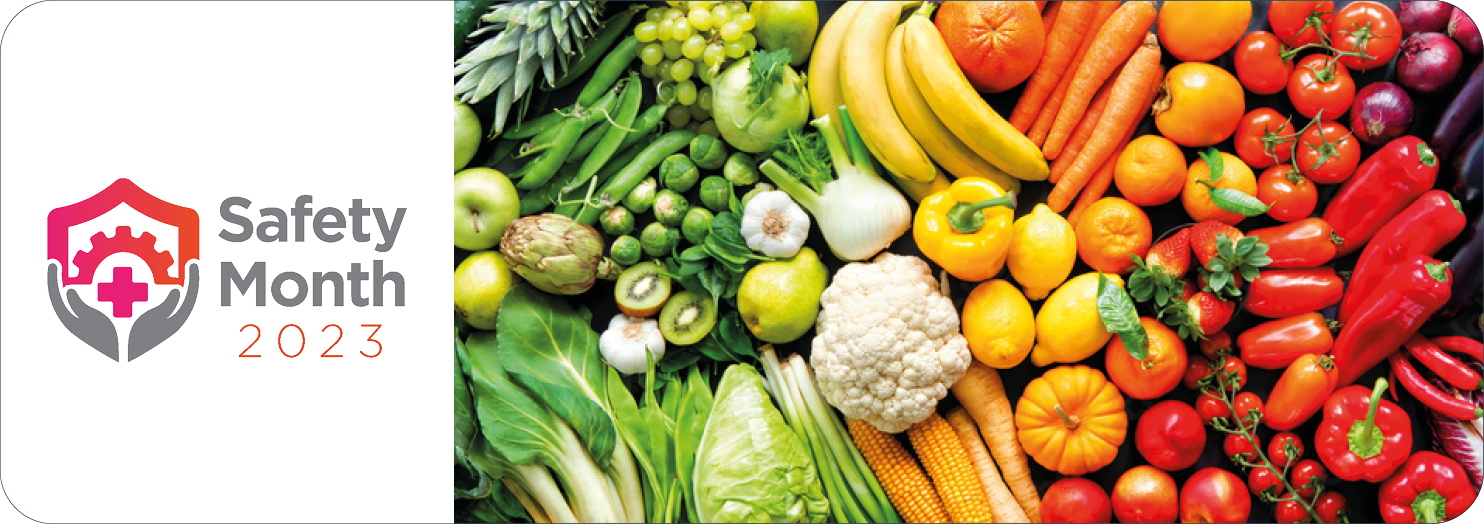
At Devro, we care about our employees’ health and safety. Throughout October, we celebrated Safety Month as part of our ongoing effort to achieve a Zero Harm community.
This year’s Safety Month was a tremendous success, with each of our 7 sites across the globe engaging in a variety of activities, and we made sure to include our remote workers in every possible way.
Each week, we hosted webinars tailored to our remote employees, focusing on important topics such as Road & Pedestrian Safety, our Employee Assistance Programme, and Safe Work Practices from Home. We also published articles on our intranet each week, providing a deeper understanding of these key subjects and providing links to valuable resources.
Bathurst (Australia) carried out a variety of training courses on topics such as Confined Space, Working at Height and First Aid and held a coloring competition for our employees’ families so they too could be part of Safety Month. In Gendt (Netherlands) they had forklift training, workshops on how to report accidents and celebrated eight years without a LWDI (Lost Working Day Injury) – a huge achievement!
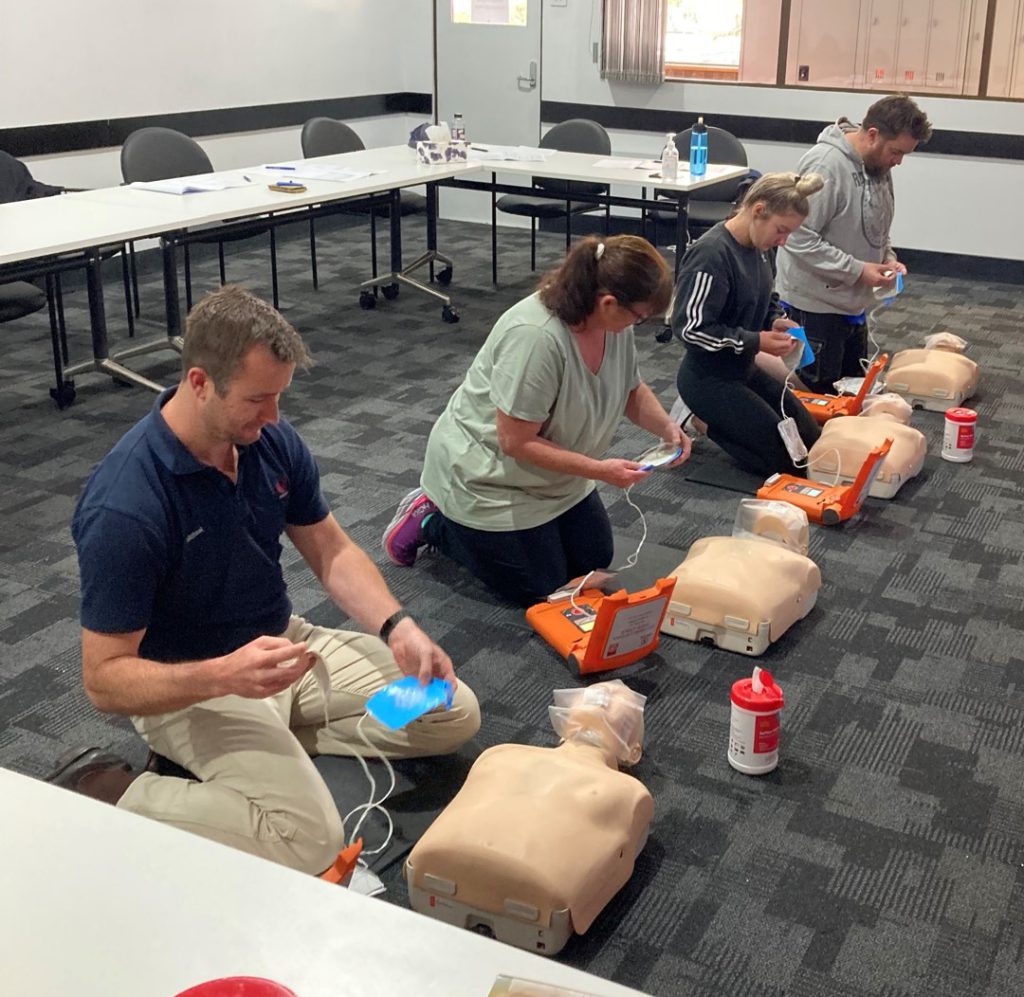
In the Czech Republic at our Jilemnice site, ‘Fresh Fruit Fridays’ were highlighted to help encourage healthy habits as well as a workshop for all employees focusing on ‘My Body, My Health, My Life’ which covered all essential information on preventing lifestyle diseases and self-examination tips.
Moodiesburn’s Safety Champions (Scotland) proactively arranged for custom insole measurements to prevent plantar fasciitis, as well as offering flu vaccinations and comprehensive health checks. In Nantong (China), Basic Life Support training provided by Ruici Hospital was carried out, and a Safety drawing contest engaged our employees’ children, with the winning drawing set to feature in the 2024 Devro calendar.
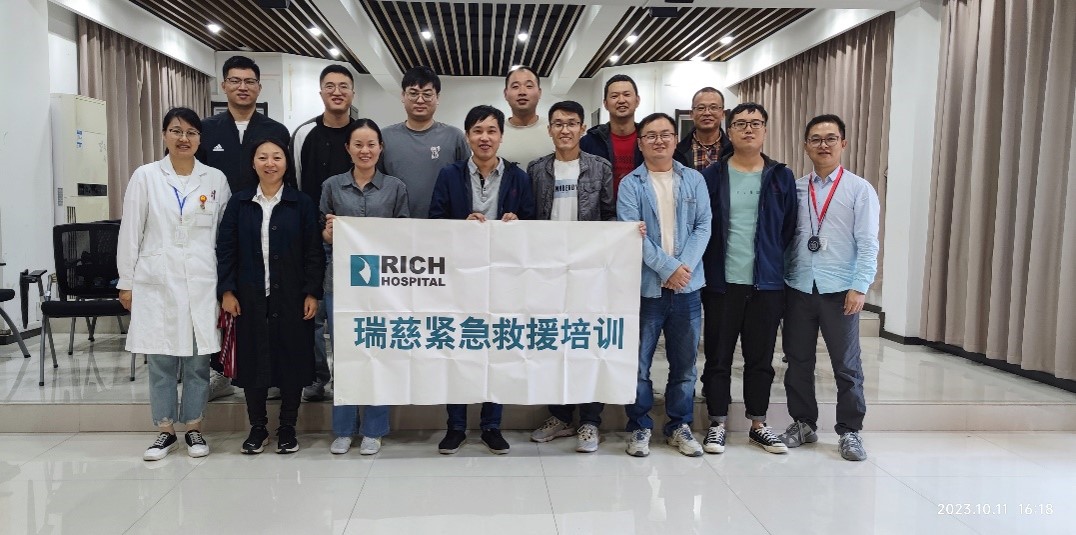
Finally, at Sandy Run (USA), all staff were invited to attend mental health training sessions every week, maintaining our focus on promoting healthy hearts and minds. We also made flu vaccinations available throughout the month to protect our employees. All in all, a busy month full of wonderful activities highlighting the importance of Health and Safety and reaffirmed that safety is a responsibility we all share.
Bioiberica at the CPHI trade fair in Barcelona
CPHI is one of the most important human health fairs in the world.
This year it was held in Barcelona, Bioiberica’s home town.
Bioiberica showcased its leadership in scientific research, sustainable development and strategic partnerships for a more resilient future with its portfolio of Active Pharmaceutical and Nutraceutical Ingredients.
The “O” in Sinova: Great potential in oleochemistry
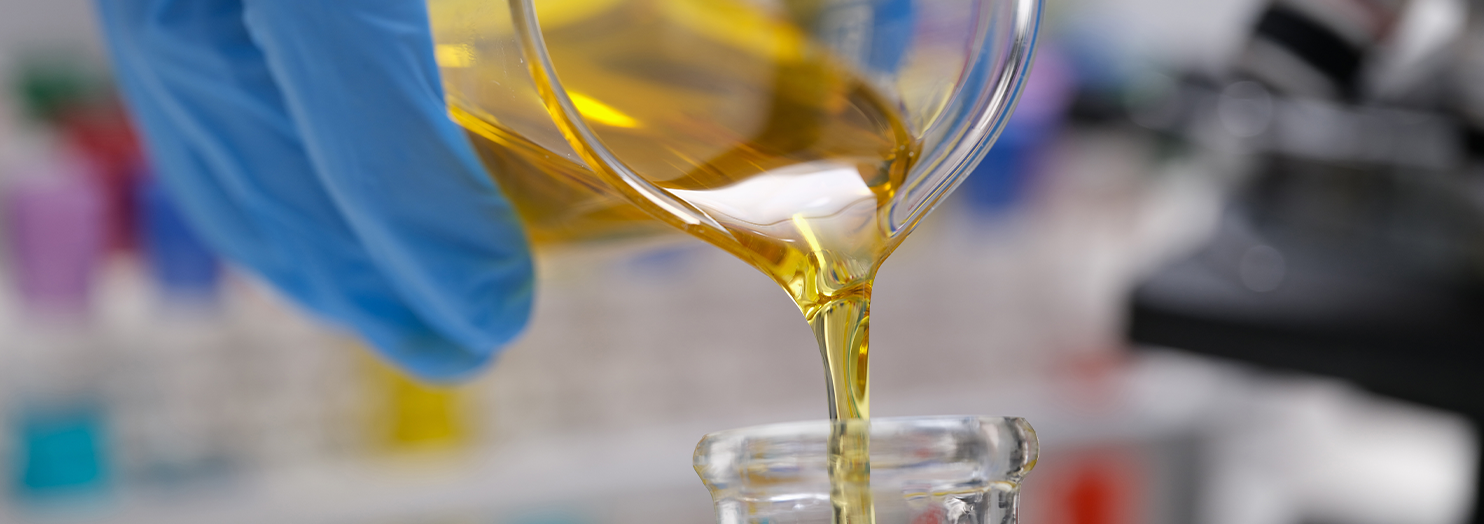
The “O” in Sinova stands for the oleochemical industry, one of the most important markets for our Sinova fats.
Producing for the oleochemical industry means that the soap or the washing powder we all use in our everyday life, can be made from the fats that Sinova processes.
How is this possible?
Sinova only collects animal by-products that have been declared fit for human consumption at the point of slaughtering (after undergoing veterinary checks) – these are the so-called C3 materials. From these materials we produce a wide range of fats that can be used in the composition of various consumer products.
An essential ingredient
Our products are at the center of the current ambition to reduce our ecological footprint. In fact, our animal fats, like vegetable oils, are one of the basic raw materials from which many of the ingredients for the production of our everyday consumer goods are derived.
They undergo a long chemical transformation process during which oleochemical manufacturers extract the components needed to manufacture their products. Just to illustrate the broad variety of applications, this includes e.g. detergents, paints, solvents, lubricants, plastics, biofuels, aircraft de-icers, cosmetics and the famous hydroalcoholic gel used for hand disinfection to prevent the Covid virus. These organic raw materials are an effective ingredient that is gradually replacing petroleum-based products. They now account for 3% of global consumption (compared to 97% from fossil fuels).
What factors determine the final use?
A large part of our fat production goes into oleochemicals, animal feed and biofuels. Here, the market situation will determine the final direction. More precisely, it is the price level for fat that determines the industry that will finally use the fat from Sinova. The task of our sales teams is therefore to optimise the Sinova sales by anticipating changes on the global markets as good as possible.
A challenge for the future
In a world whose energy needs have doubled in 20 years, the production of oils and fats has reached 200 million tons per year. Animal fats account for around 12% of global production.
It is necessary and important to work on their development and further valorisation. At Sinova, we are thriving to contribute to this change that is so important for our sustainable future!
Close to action – Sinova Townhall Meetings
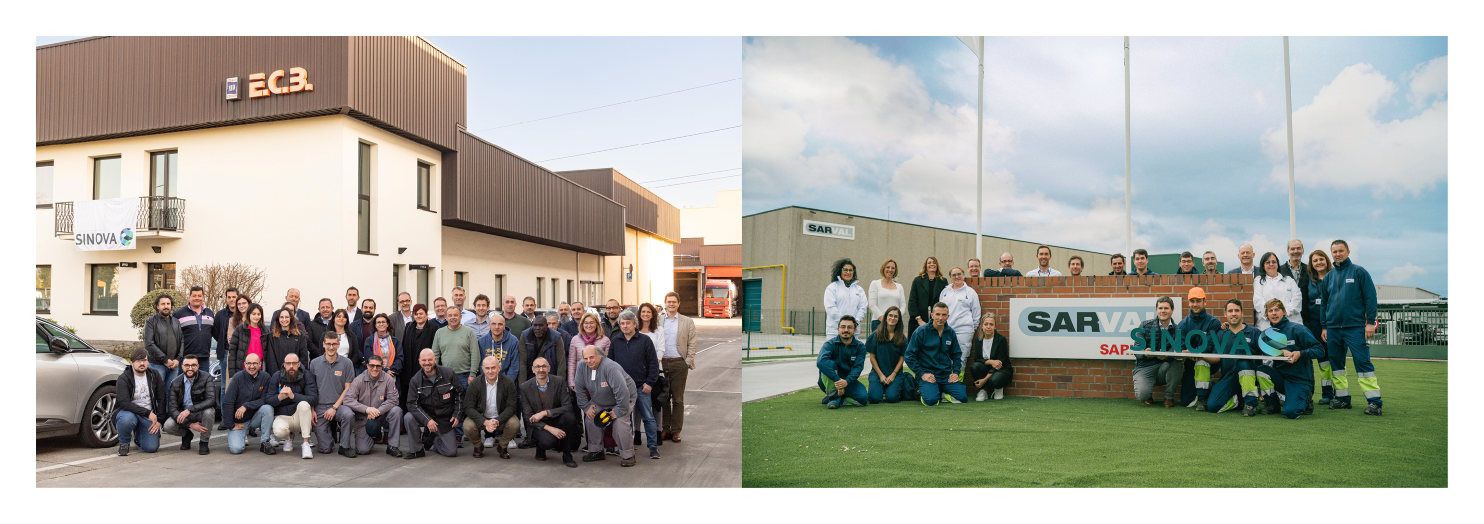
At Sinova we live the principle of being ONE international team.
It is very important to the Sinova Board that this mindset is practiced and actively embraced at all levels so that every colleague is included. Therefore, the Sinova Board visits various Sinova sites on a quarterly basis to further strengthen the exchange with the colleagues but also to have an open ear to the challenges and questions that may arise in our team.
The Sinova Board consists of Andy Plews, Arnaud Becard, Emmanuel Layous, Lars Krause-Kjær, Nicolas Bonnaud, Peter Hill and Thorsten Seeger. In addition to the online meetings that the seven have on a weekly basis, a face-to-face meeting every three months in one of our factories is an important element in the communication between the different areas of our Sinova division. The aim of these meetings is to be close to the operational business and its colleagues, as well as to deepen our Sinova strategy that we follow for more than two and a half years.
A central part of these face-to-face Board Meetings is a visit to a Sinova factory. Along with a tour through the production facilities, there is also a Townhall Meeting. These Townhall Meetings last about an hour and invite all available colleagues to an open exchange with the Board. All colleagues have the opportunity to raise ideas, challenges or questions within an open dialogue. The Board members believes that every opinion in our ONE team is valuable and important, and everyone is invited to play an active role in our Sinova journey. Especially through the colleagues from operations, we can gain new and enriching ideas and views.
After various Board Meetings in France and Italy, the time had come again in November 2023 for a visit in Spain.
In Spain the Board Meeting was held in our Segovia factory. Following a warm welcome and an informative factory tour, another animated Townhall Meeting took place. Exchanging ideas with the Sinova Board helped to clarify and discuss many questions, and the Board was able to take away valuable ideas and inspiration from these days in Segovia.
The Sinova Board is looking forward to the upcoming town hall meetings in 2024 so that an open exchange with our committed colleagues will take place as well in other regions of our Sinova division.